Friction Management
PTFE NanoGLIDE® has been Friction Tested and Studied with Amazing Clarity in Textile Fabrics.
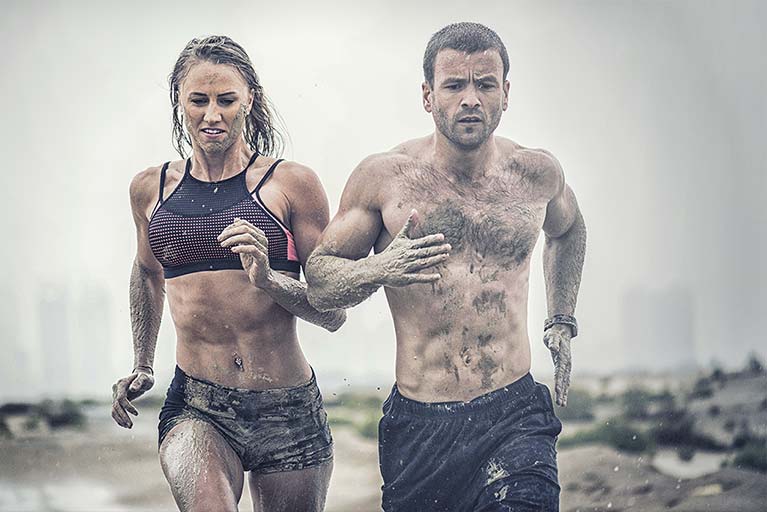
What is friction as it relates to a textile fabric and physical activity?
Frictional forces that oppose the movement of material across the skin cause an increase of blisters, moister/sweat, chafing, and redness seen in physically active individuals.
When the skin is in contact with an object (e.g., shoe, sock, base layer, prosthetic device) and an external force attempts to move the object across the skin, a frictional force (Ff) will oppose the movement. As the external force increases, friction increases, and movement will occur when the external force exceeds the Ff. The magnitude of the frictional force is proportional to the normal force (Fn, force of contact, or perpendicular force) according to the formula Ff=μ*Fn, where μ= coefficient of friction.
All the published studies and characteristics referenced below indicate that when the friction coefficient is smaller, the corresponding shear stress will be lower on the skin surface for moisture, chafing, hot spots, and blistering. However, the higher acceleration and greater centripetal force in the reverse will cause greater skin/fabric interactions and increased sweat/moisture.
Fabic Tests & Reports
All test reports from MSC contain a TS designator. 1-4 below
Various fabrications with PTFE (NanoGLIDE®) were independently tested at MSC in North Carolina.
Learn More01.
TS 89820, TS 89821, TS 89822, TS 89823 and TS 89824
5 fabrics with varying %’s of the PTFE technology were independently tested for similarities:
- Vertical Wicking
- Absorbency
- Martindale Abrasion
2 samples of each fabric were tested.
Average Vertical Wicking for all 5 were +-16 cm, Average Absorbency for all 5 were +-1.0 sec, and the Average Martindale Resistance was +-50,000 rubs with no hole.
The test was stopped at failure or 50,000 rubs and all fabrics were tested at the same time.
The data demonstrates that all fabrications have consistently good abrasion control, good vertical wicking, and good absorbency with PTFE.
02.
TS 65957 was a 100% PTFE knit, and TS 65958 was a placebo control knit with same denier of yarns but no PTFE.
The PTFE knit was stopped at 100,000 movements because no hole appeared, but the placebo control failed with an average of 62,775 movements before a hole.
There was a 37% improvement in abrasion properties.
However, the test was also stopped at 100,000 movements. When the failure would have occurred is unknown. There was no immediate sign of failure and because of the long machine run time, it was concluded 100,000 movements were enough to demonstrate the value of PTFE.
3 samples of each knit were tested and both fabrics were tested on the same day.
This data demonstrates enhanced abrasion control with PTFE, but also the ability to reduce hot spots, friction, chafing, and chances of blistering for a piece of fabric or sock on the skin surface.
03.
TS 108329 was a placebo control knit with a 2/70/17 Nylon 66, and TS 108328 was a PTFE 2/70/17 Nylon 66.
The placebo failed with an average of 12,639 movements before a hole, and the PTFE failed at 27,968 movements before a hole.
There was a 55% improvement in abrasion properties
Both fabrics were tested at the same time.
This demonstrates the enhanced abrasion control of PTFE for reducing hot spots, friction, chafing, and chances of blistering from a piece of fabric or sock on the skin surface.
04.
TS 45270 was a 2 ply 70/34 Nylon PTFE knit sleeve, and TS 45274 was a 2 ply 70/34 Nylon control knit sleeve.
The PTFE yarn has less drag, the PTFE average movement before a hole was 1,391 cycles vs. 154 cycles for the placebo knit, the absorbency was within a margin of error +-.30 sec, the drying rate was .0015 g/min better with PTFE, the PTFE had a vertical wick at 10.0 cm at 30 min vs. 8.8 cm at 30 min for the placebo control.
There was an 88% improvement in abrasion properties.
Conclusion of test reports
The only data from MSC that can be qualitatively and quantitatively measured is “abrasion control”.
PTFE is well documented when wet or dry to improve abrasion control. This would translate very favorably in the above fabrications whereby a wearer could expect improved wear and tear of the fabric, improved abrasion control, reduced hot spots, blistering, or chafing on the skin surface. These are attributes to consider when putting PTFE yarns into textile products.
Wicking and absorbency can vary depending on the product; sock, base-layer, shoe fabric, outerwear fabric, football jersey etc., and the PTFE, or non-PTFE yarns used.
Many standardized ASTM and AATCC test standards for absorbency, wicking, and dry times are a one size fits all approach to textiles and excludes other variables such as yarn twist, air tack, denier size, resin, surface area, chemistry applied during manufacturing, etc. and therefore makes it almost impossible to decide what a pass or failing grade should be, or what it means by establishing an arbitrary number from a measurement. These tests do not take into consideration how air permeability, wicking in the horizontal, and moisture or vapor transmission can impact (or not) evaporation and drying of a textile fabric.
These are attributes to consider when putting PTFE yarns into textile products.
- Abrasion properties can be both qualitatively and quantitatively measured in various fabric constructions with these MSC test reports.
- What about vertical wicking or absorbency? These results from MSC are subjective at best.
- For a better understanding of more advanced test methods please review the Activewear-Dynamics (AD) testing and results for evaluating qualitative and quantitative data for wicking, moisture movement, vapor, and evaporation.
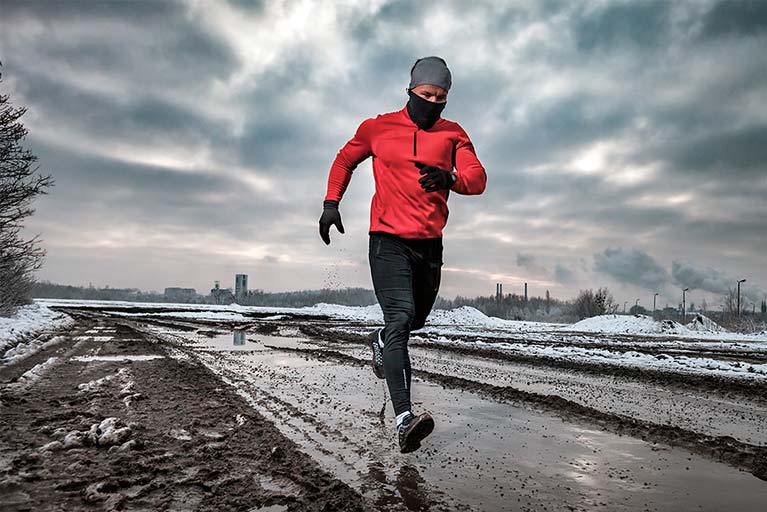
Moisture Management
The process whereby fabrics enable sweat to move from our skin through our layers and finally, into the environment.
Learn More